Nøsted &'s Kragerø division is more than just a workplace—it is a hub of collaboration, innovation, and craftsmanship. Here, several of Nøsted &'s renowned FRAM products are manufactured, carrying forward a legacy of over 110 years built on quality and reliability.
Meeting Preben at the Production Entrance
We meet Preben at the factory entrance. He has been a part of Nøsted & since 1998 and is now the site manager for the Kragerø factory. Preben takes us on a tour of the production area, explaining how the factory has evolved over time.
– Instead of traditional departments, production is organized by processes. We have process managers overseeing each key stage of production and specialists responsible for areas such as quality and machine maintenance, he explains.
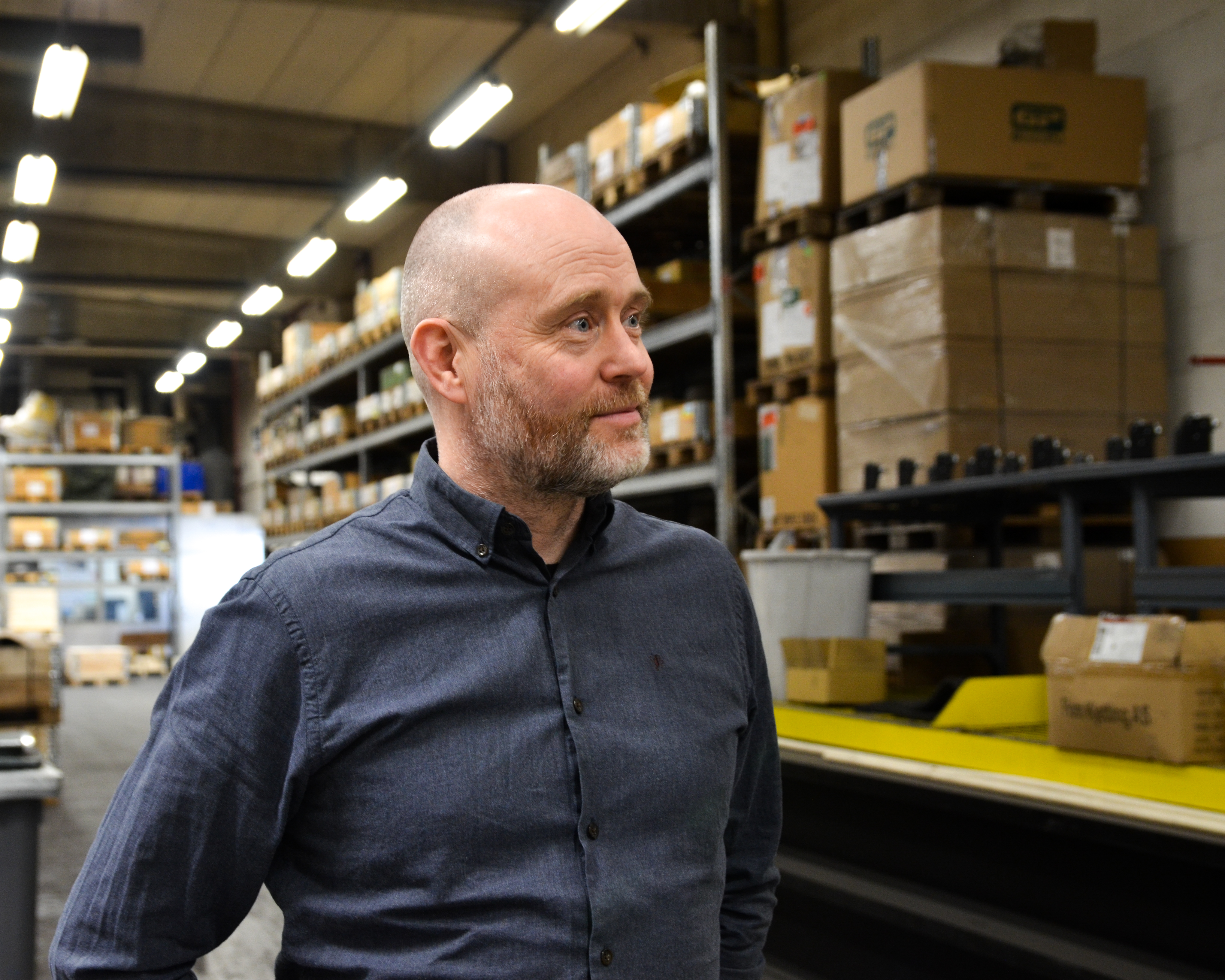
An Inclusive and Positive Work Environment
During the tour, we meet Inger Lise Stenvik, who works on building and assembling equipment. She describes her workday as varied and structured.
– It is important to ensure that everything is properly documented so that we can track the product throughout the entire production process, Inger Lise says with a smile. She highlights the positive work environment as a key factor in job satisfaction.
– When I started here, I was warmly welcomed. My colleagues are cheerful, friendly, and inclusive, which makes for a great working atmosphere, she says.
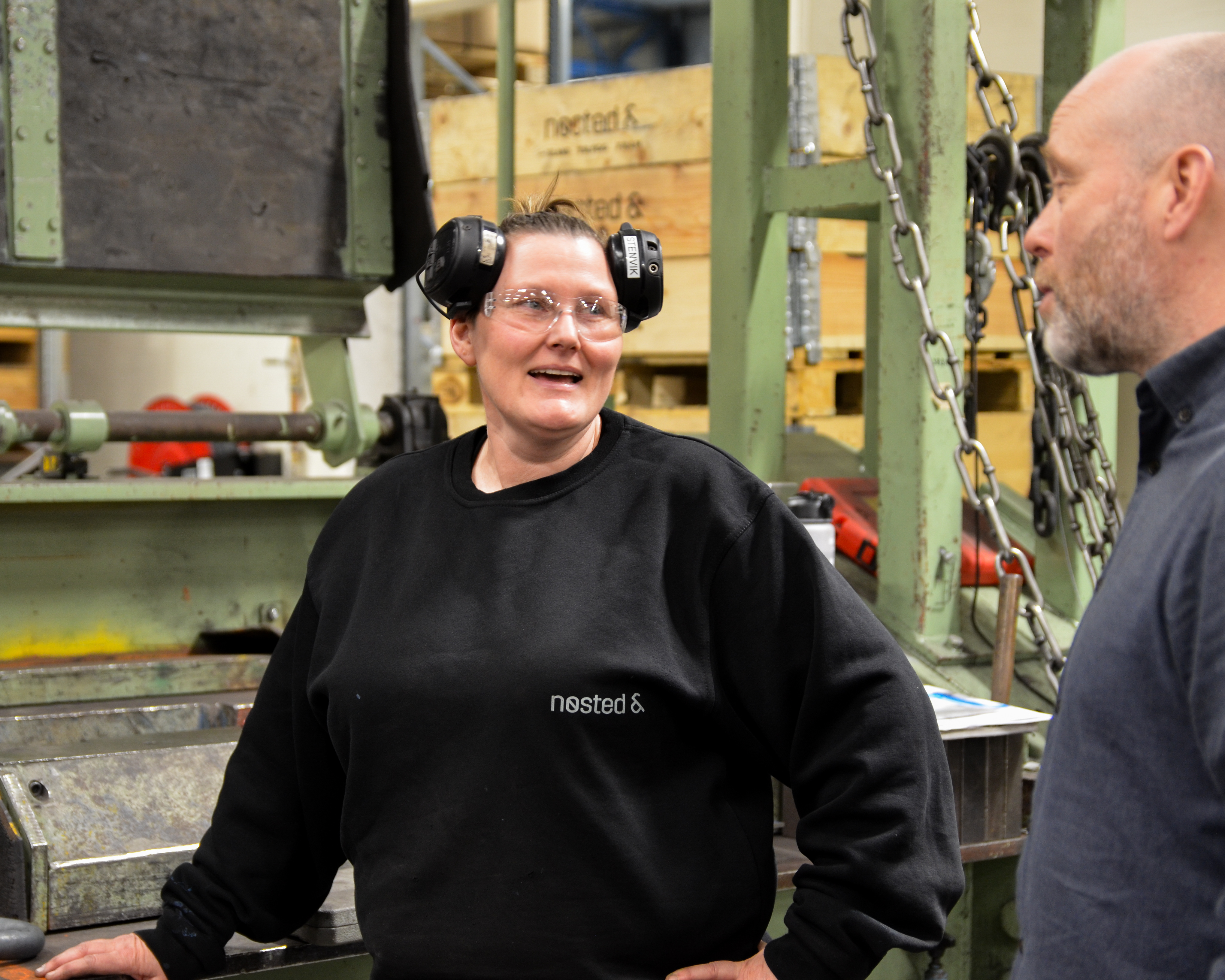
Jonas in the Production
We move further into the facility and meet Jonas Andreassen, the newest addition to the team. He operates the cutting machine in production and often works independently but receives support when needed.
– I have been warmly welcomed and have learned a lot, he says. Jonas is the second generation working at Nøsted &, and his father, Martin, has become a good colleague.
– I originally planned to become a carpenter but realized that career wasn't the right fit for me. Fortunately, I was familiar with Nøsted & and secured a position here, which has been a great match.
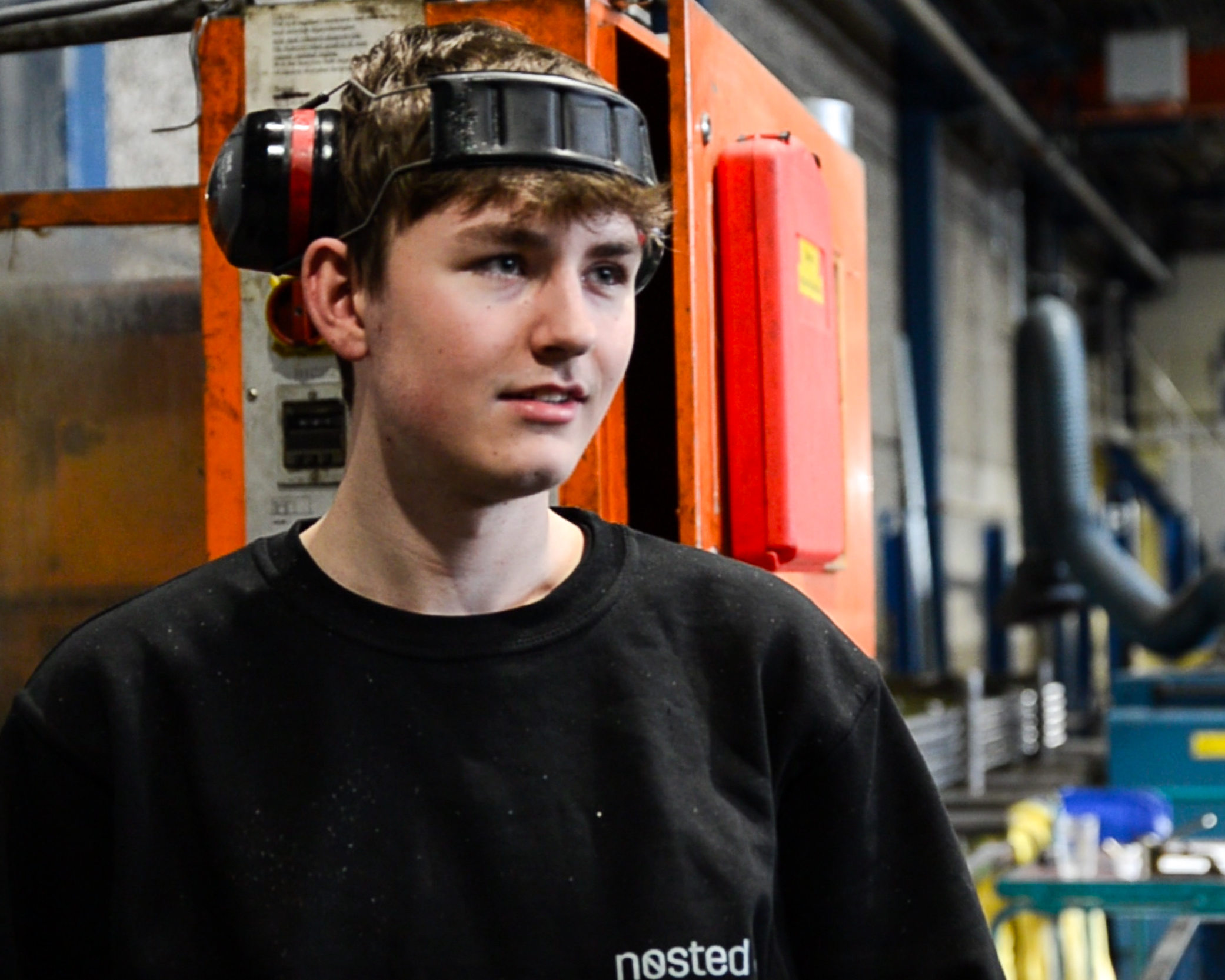
Competence Development
To ensure the right competence development, the factory has created a competence matrix that outlines skill levels for different machines and processes. – This system helps us structure training and ensures that we have the right expertise in the right places, says Preben.
From Production to Technical Specialist
We also meet Martin Andreassen, who has worked at Nøsted & for 14 years. Martin has transitioned from production to an office-based role and is now a technical specialist in heat treatment and machine welding.
– I now prefer working with my head, but I also understand how crucial precision is in production, he says. He highlights the increasing focus on health, safety, and the environment (HSE) over the years and how safety measures are always prioritized. Martin also notes a clear improvement in product quality, thanks to more automated systems ensuring precision.
– If you show that you're willing to take responsibility, you will be given responsibility, says Martin.
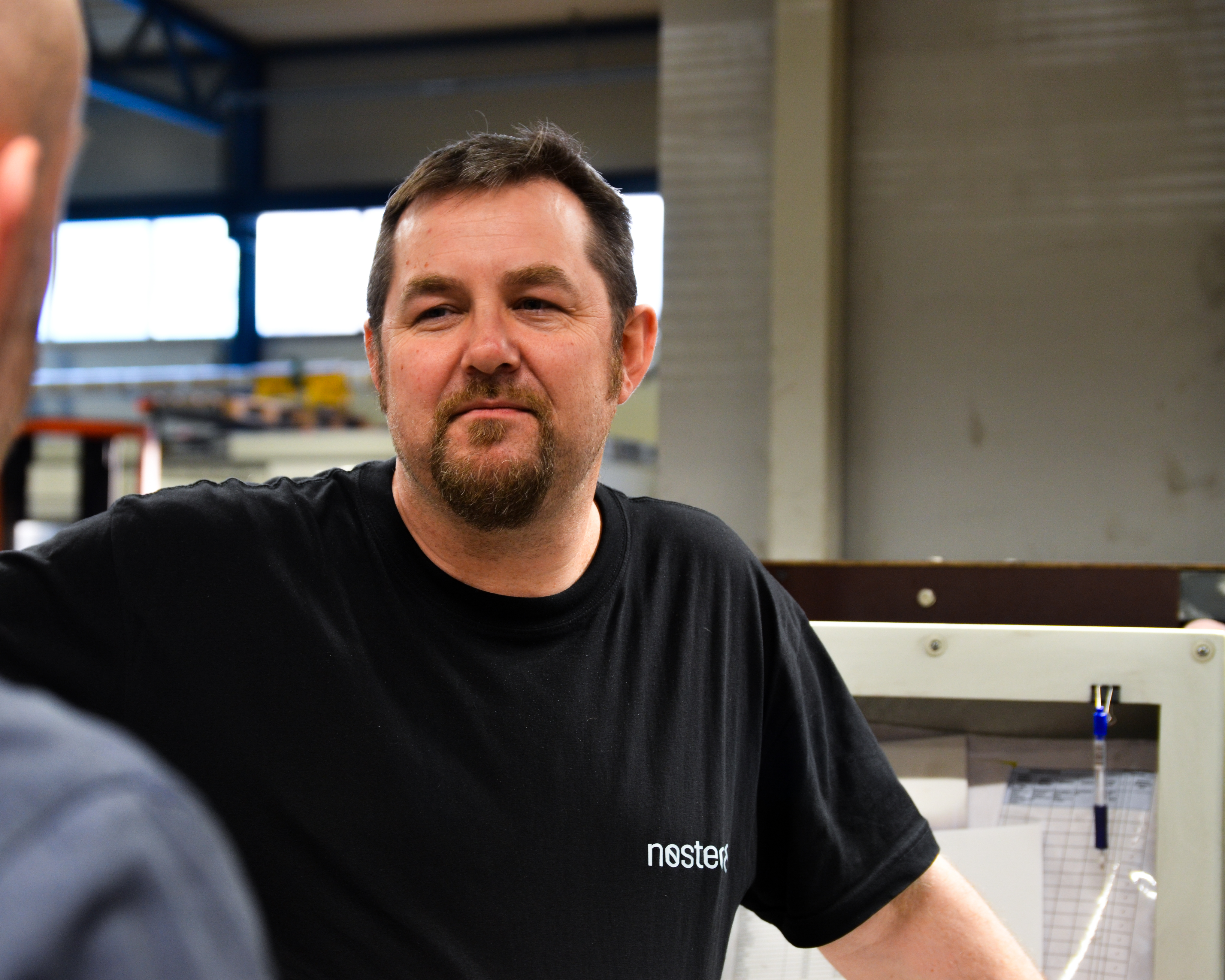
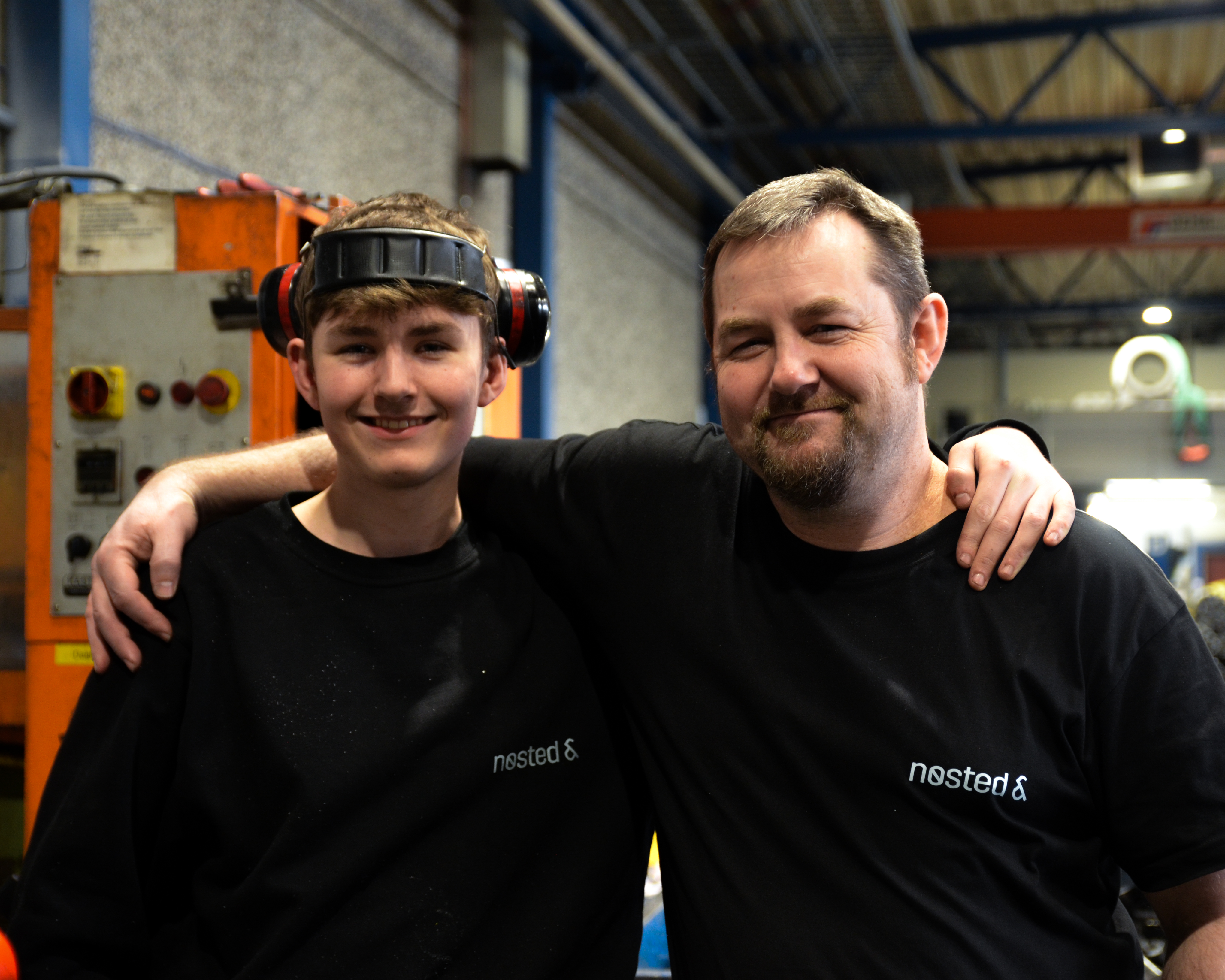
Billy in the Workshop
In the workshop, we meet Billy Pedersen, who works with machining. He appreciates the variety in his work and the collaboration across teams.
– My work is very diverse. Each day, I review which tasks need prioritization and take it from there, he says. He emphasizes that teamwork is essential and that quality is always a priority.
– If I go through a whole workday knowing that everything I delivered is of high quality, I go home feeling satisfied, says Billy.
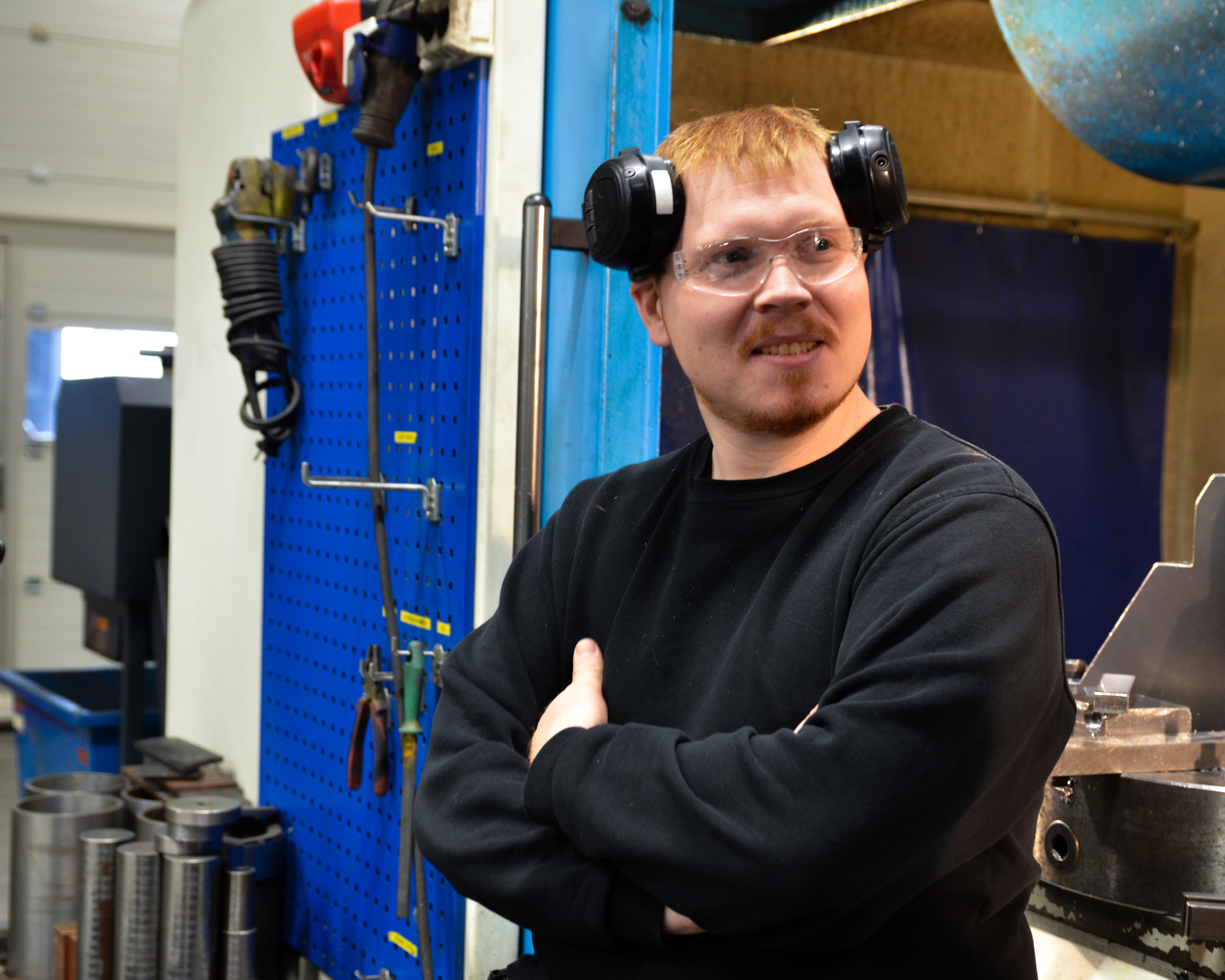
If I go through a whole workday knowing that everything I delivered is of high quality, I go home feeling satisfied
Sustainability and Efficiency
Sustainability is an important part of the factory's operations, and Preben highlights that the facility is ISO 14001 certified. – We have reduced energy consumption, installed solar panels, and implemented energy meters to identify high-energy-consuming processes. Additionally, we have optimized the powder coating process and introduced a cardboard compactor to reduce waste, says Preben.
The Road Ahead
Preben sees great potential for further automation in the factory. – We have already made significant progress, but there is still more potential to explore. We also want to leverage expertise across the company more effectively by fostering closer collaboration between our factories in Mandal, Kragerø, and Lithuania. This way, we can share experiences and become even more efficient, he concludes.